On March 20, 2023, the Automotive Electronics Council (AEC), the standards body for automotive electronic components, published Rev E of AEC-Q200, Stress Test Qualifications for Passive Electrical Devices. The new AEC-Q200 Revision E standard adds fuses to the list of components that can be AEC-Q200-qualified so that the fuses meet a high standard for ruggedness and reliability. Revision E provides a single standard that manufacturers can use to design and test fuses for the automotive market. The fuses must meet a rigorous set of more thorough tests that apply more significant stress than the tests required by standards for fuses from nationally recognized test laboratories such as UL and CSA.
The standards define the compliance requirements that qualify components that can withstand both the harsh automotive environment and extremes in the external environment. The components must pass environmental stress tests such as temperature cycling and humidity. In addition, the components must pass physical stress tests such as shock and vibration.
Littelfuse is the first automotive fuse manufacturer to introduce multiple AEC-Q200 Revision E-qualified fuses, including cartridge fuses, surface mount thin film chip fuses, high current surface mount fuses, and ceramic, fast-acting leaded fuses. View the video.
Needs for fuses in automotive vehicle circuits
The addition of electronics technologies into automotive vehicles has been extensive and is continuing. The substantial quantity of electronic circuitry requires individual overcurrent protection in each circuit. Fuses are needed to protect the battery monitoring system (BMS), the on-board charger (OBC), the power distribution unit (PDU), the traction motor inverter, the communication circuits, and the vision circuits. Figure 1 shows the wide range of circuits in electric vehicles and lists the types of fuses needed for these circuits.
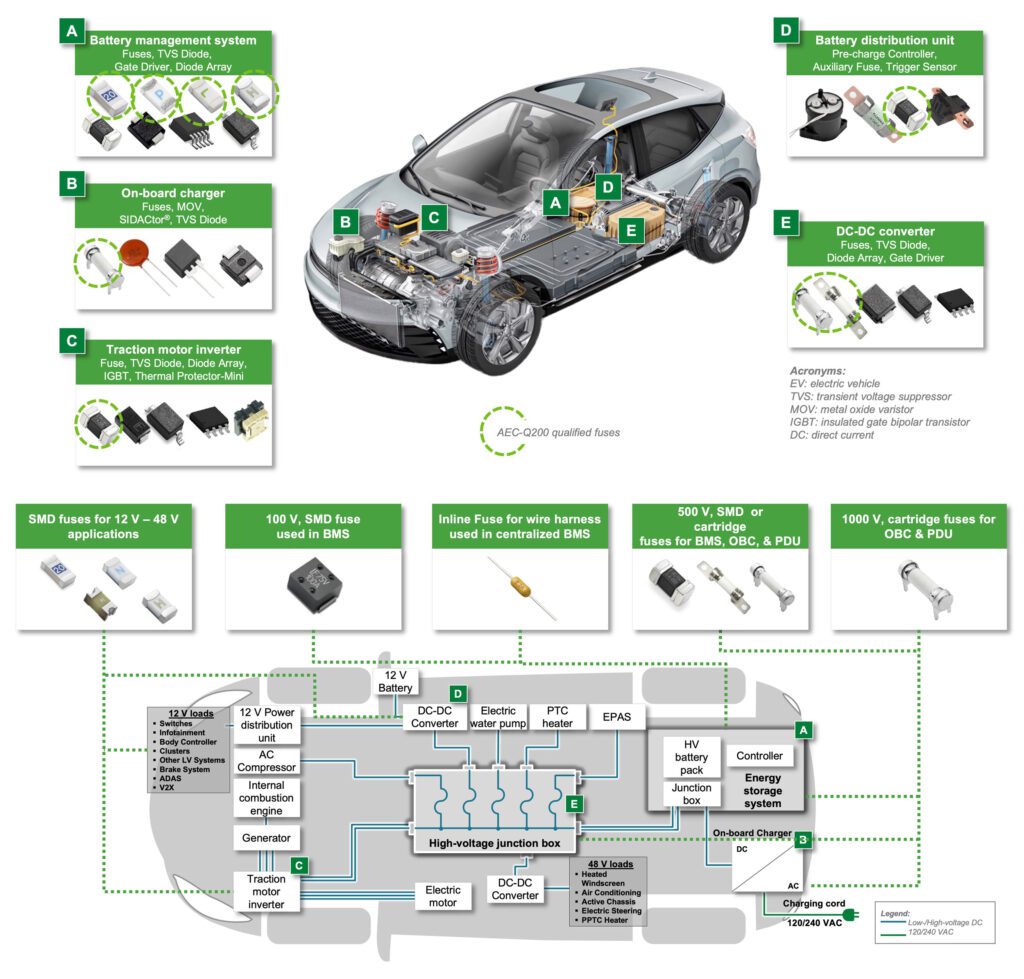
AEQ-Q200 Rev E Test Standards
Figure 2 (top) describes the types of tests that the AEC-Q200 standard requires components to pass. The tests fall into two categories: environmental stress and physical characteristic stress. The environmental stress tests involve testing at high temperatures, cycling the fuse through a wide temperature range, and testing at high humidity. The physical stress tests include mechanical shock, vibration, flammability, resistance to solvents, strength of the fuse terminals, and withstanding the heat from soldering.
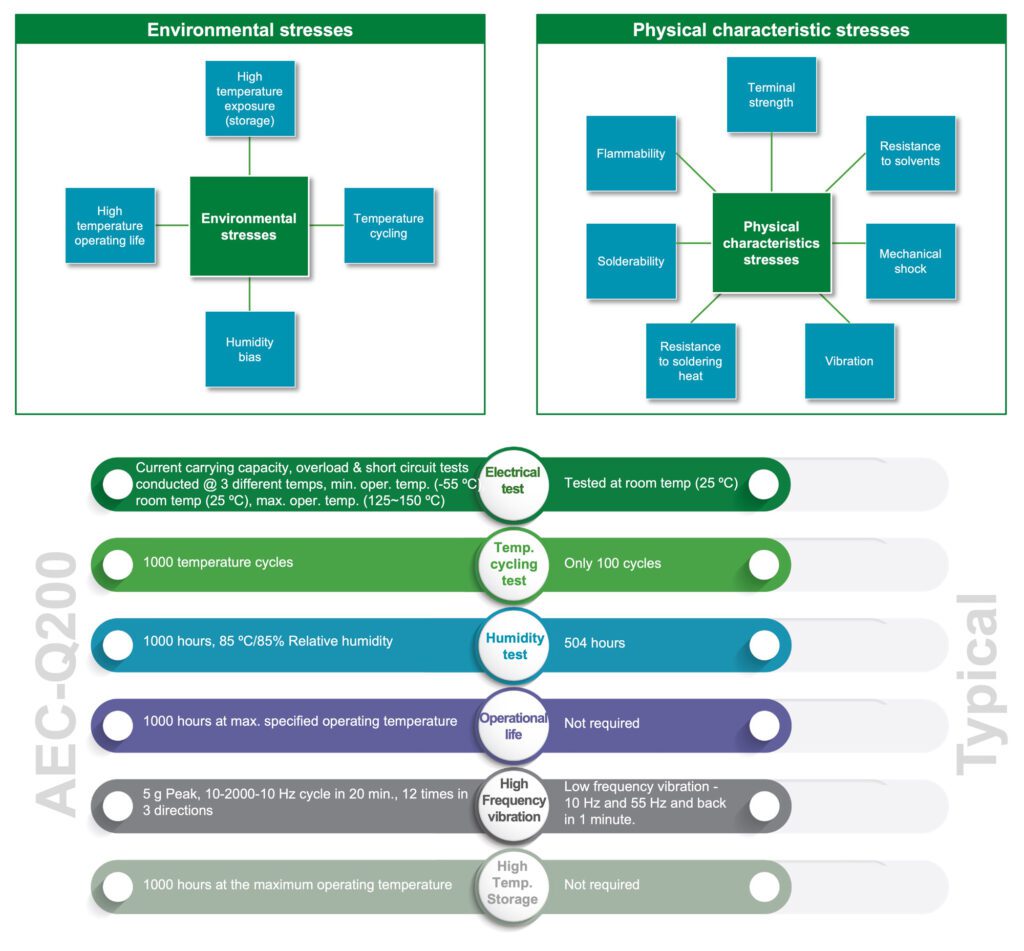
Figure 2 (bottom) gives examples of the AEC-Q200 Revision E stress tests that exceed the requirements of typical fuse test plans. In some cases, the typical test plan does not even include an AEC-Q200 Revision E test. In other cases, the new AEC-Q200 Revision E test has a 2x to 10x more difficult requirement than a typical fuse test.
Littelfuse AEC-Q200 Revision E Qualified Fuses
Littelfuse has a complete portfolio of AEC-Q200 Revision E-qualified fuses. The portfolio includes cartridge fuses, surface mount fuses, and ceramic fuses.
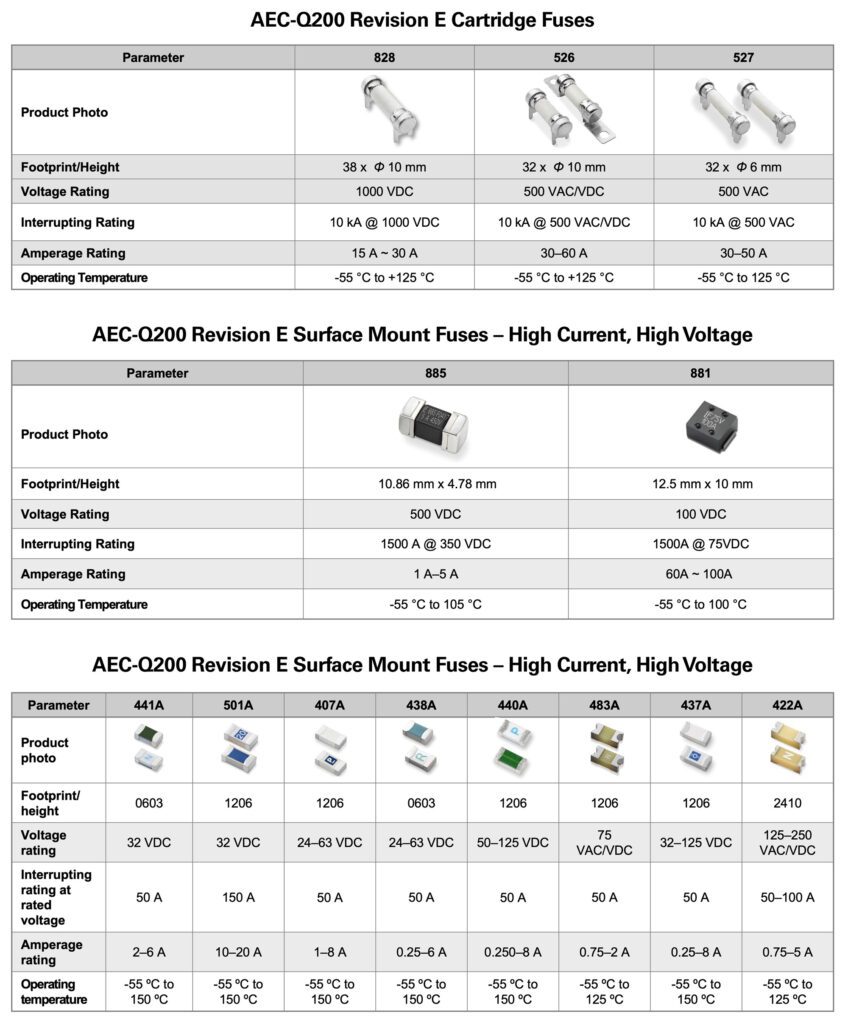
Cartridge fuses
The 526 series, 527 series, and 828 series cartridge fuses shown in Figure 3 (top) have current ratings from 15 A to 60 A, with 500 V and 1000 V voltage ratings. The fuses have interrupting ratings of 10 kA and can operate in a temperature range from -55° C to +125° C. They have end caps with integrated stand-off leads or bolt-down options to eliminate the need for mounting accessories or lead-forming processes. These fuses can provide overcurrent protection for on-board charger circuits and the power distribution unit.
Surface mount fuses
Littelfuse has an extensive line of AEC-Q200 Revision E surface mount fuses. The 885 series and 881 series fuses shown in Figure 3 (middle) can operate in high-voltage circuits with 100 V and 500 V ratings. The 881 series fuses have current ratings up to 100 A. Both series have an interrupting rating of 1500 A. These compact fuses can protect Li-ion battery modules in battery packs.
An additional eight families of surface mount fuses are also shown in Figure 3 (bottom). These space-saving fuses have current ratings from 0.25 A to 20 A. The fuses can operate in circuits with voltages up to 250 V. Their operating temperature range, -55° C to 150° C, is the highest of all the AEC-Q200 Revision E fuse families. Use the surface mount fuse families in a wide range of automotive circuits, including the battery management system, the high voltage DC-DC converter, the automotive navigation system, the sensor circuits, the thin-film transistor display system, and the entertainment systems.
Ceramic fuses
The PICO® II 521 ceramic fuses are a very fast-acting fuse series. They have current ratings between 2 A and 7 A. The 75 V rating allows use in circuits that operate up to that voltage. These fuses will interrupt a 200% overcurrent in 1 a maximum of 1 second. They can interrupt an overload up to 300 A. The 8 mm long x 3.4 wide body saves printed circuit board space and can perform over the -55° C to +125° C temperature range. The PICO II 521 fuses can provide overcurrent protection for battery management system electronics and wire harnesses.
Most extensive portfolio of AEC-Q200 Revision E qualified fuses
Littelfuse has a broad fuses portfolio that is AEC-Q200 Revision E qualified for the automotive market. With current ratings from 2 A to 100 A and voltage ratings to 1000 V, Littelfuse has rugged, reliable, stress-tested fuse for every automotive application. Automotive designers can reduce qualification time for meeting the new requirements of the AEC-Q200 Revision E standard, and they can quickly identify Littelfuse overcurrent protection fuses to meet all their requirements.
For more information, visit the AEC-Q200 Revision E Qualified Fuses page and Updated AEC-Q200 Specifications for Automotive Applications presentation at Littelfuse.com.
For a quick introduction to the AEC-Q200 fuse portfolio, view the video.
Learn more:
- Benefits of advanced isolated package in high-power battery charging design
- Advanced Charging Solutions for Next-Gen Commercial EVs
- Protecting critical on-board charging circuits in next-generation EVs
- Designing DC fast chargers for next-gen EVs
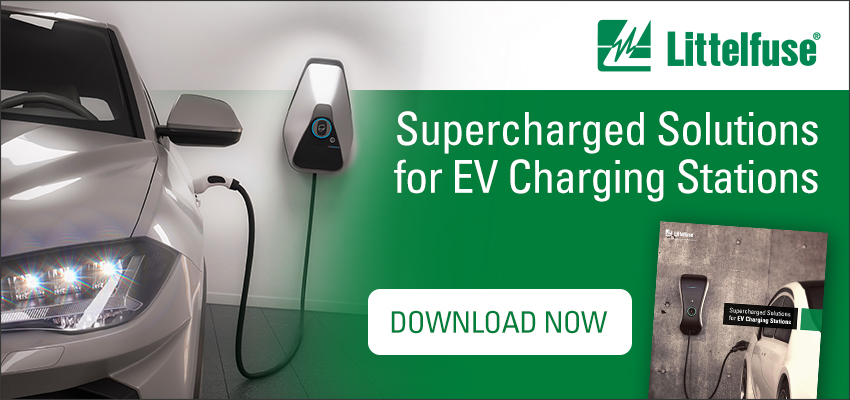
Source: Electric Vehicles Magazine